Ticketing System Case Study
GEMBO (www.gembo.co) is a leading innovator in the world of SaaS Industrial IoT Platforms, with a proven track record of delivering cutting-edge solutions that help customers achieve their business goals. The company's platform uses a combination of IoT, machine learning, and AI to provide customers with real-time insights into their operations, enabling them to make better decisions and optimize their performance. GEMBO is committed to continuous innovation, and the company is constantly looking for new ways to use technology to help its customers succeed.
Customer Intro
The customer is a multi $B Tier one manufacturer, with multiple factories around the globe. Manufacturing lines vary between electronic manufacturing to semiconductor, serving a variety of markets including Automotive, Networking, Industrial, Audio and Gaming.
GEM has deployed Precare Cloud, Precare Edge, OEE Availability and predictive analytics Package. Its footprint grew from a few machines to over 90 machines in a few of their factories.
Problem
The customer has been utilizing OEE Availability analytics to identify machines with low availability and assigning them to responsible technicians. The customer's management team has been overwhelmed with emails from technicians providing status updates on the machines after they have taken corrective actions.
The customer intends to streamline the process of monitoring machine status from the receipt of OEE Availability status to the resolution of availability issues, enabling the machines to operate efficiently based on established availability KPIs. The customer has provided the following workflow to illustrate their requirements.
The customer expects that tickets will be automatically generated for all machines with availability lower than the established KPIs and sent to the responsible technicians. The technicians must ensure that appropriate corrective actions are implemented and updates are made to the tickets until the machines are fully repaired, at which point the tickets will be closed upon validation by the technicians' superiors.
Solution
Following the discussion with the customer, GEM suggested to perform the following in the existing OEE platform to properly execute the ticketing system:
- Customer to establish OEE Availability KPIs by machines
- Configure the Rules in the GEM Rule Engine
- Generate the OEE Analytics per machine at a specified time daily
- Define the calculation process comparing the availability status per machine vs. the established availability KPI per machine
- Tickets will be triggered for all machines with lower availability vs. the established availability KPI
- These tickets will be sent to the technicians handling the machines
- Technicians will update the ticket once they have completed their corrective actions
- Managers will validate the effectivity of their corrective actions by running the OEE availability of the said machine
- Upon successful validation, managers will close the ticket
- Execute the rules and monitor the implementation
Results
The ticketing system is now an integral part of the OEE Platform, with rules set up in the Rule Engine based on the customer's workflow. The rules are designed to automate the process of generating and tracking tickets, ensuring that all tickets are properly classified and routed to the appropriate personnel. The ticketing system also includes a knowledge base of troubleshooting guidelines, which can be accessed by technicians to quickly resolve issues.
GEM and the customer are working to deploy the ticketing system and ensure it is aligned with the customer's requirements. This includes configuring the system to meet the customer's specific workflow, as well as training the customer's personnel on how to use the system.
The ticketing system will help the customer improve machine availability by providing a centralized repository for all machine-related issues. This will allow the customer to quickly identify and resolve issues that affect uptime, saving them money on maintenance costs.
Conclusions
GEMBO Precare has a set of powerful data acquisition, analytics, predictive and OEE tools for manufacturing equipment. GEMBO Precare compiles critical KPIs that can be used to easily trace back which machine or machine subsystem is responsible for a low KPI score. GEMBO Precare is also able to make predictions at equal or better than humanly possible for machine maintenance to be scheduled before a failure occurs. But most importantly, unlike other market solutions, GEMBO Precare is able to deploy its own sensors independently from any machine controller and fully connect any machine data island to the GEMBO Precare Cloud at a fraction of the cost of a new machine; hence, saving manufacturers from having to make large and risky CAPEX and OPEX investments for new machines.
Contact Us
Visit us at www.gembo.co or contact us via email at sales@gembo.co
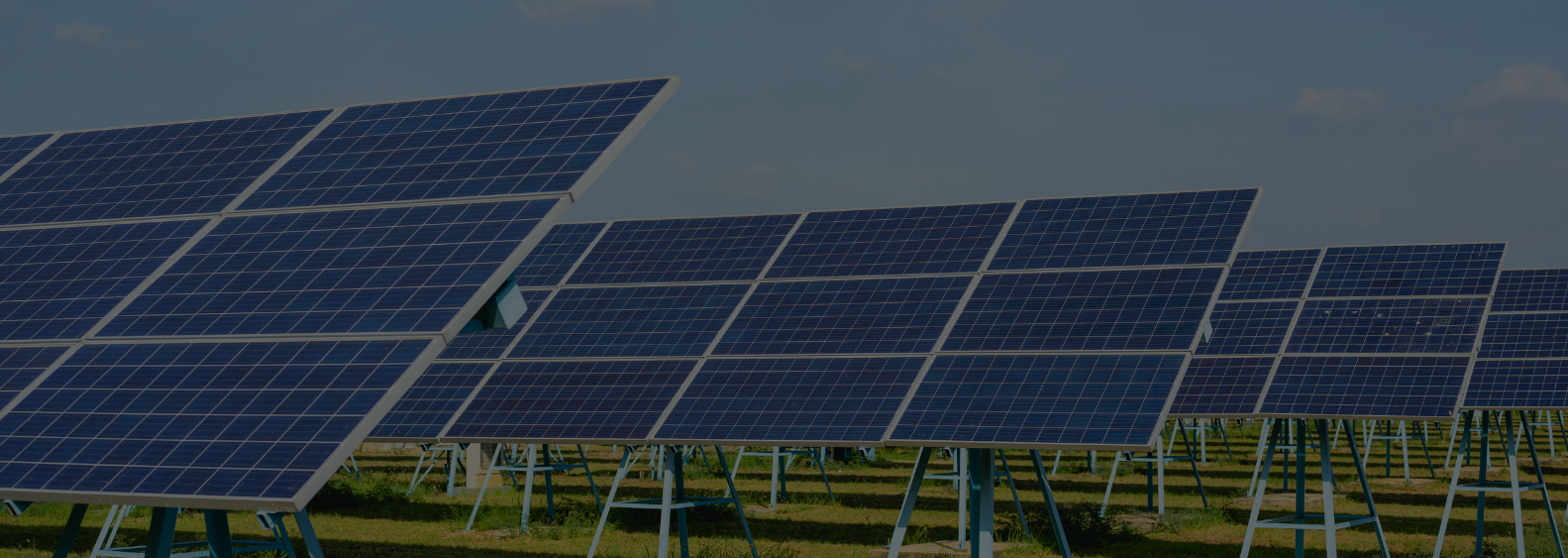
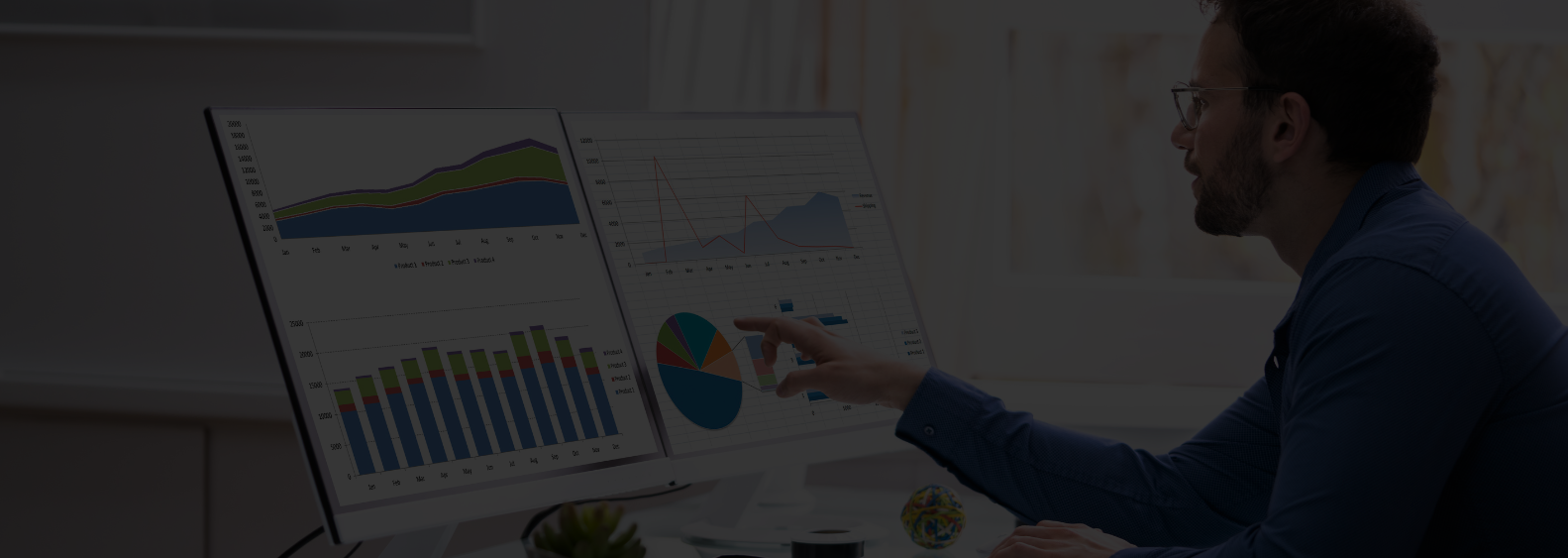
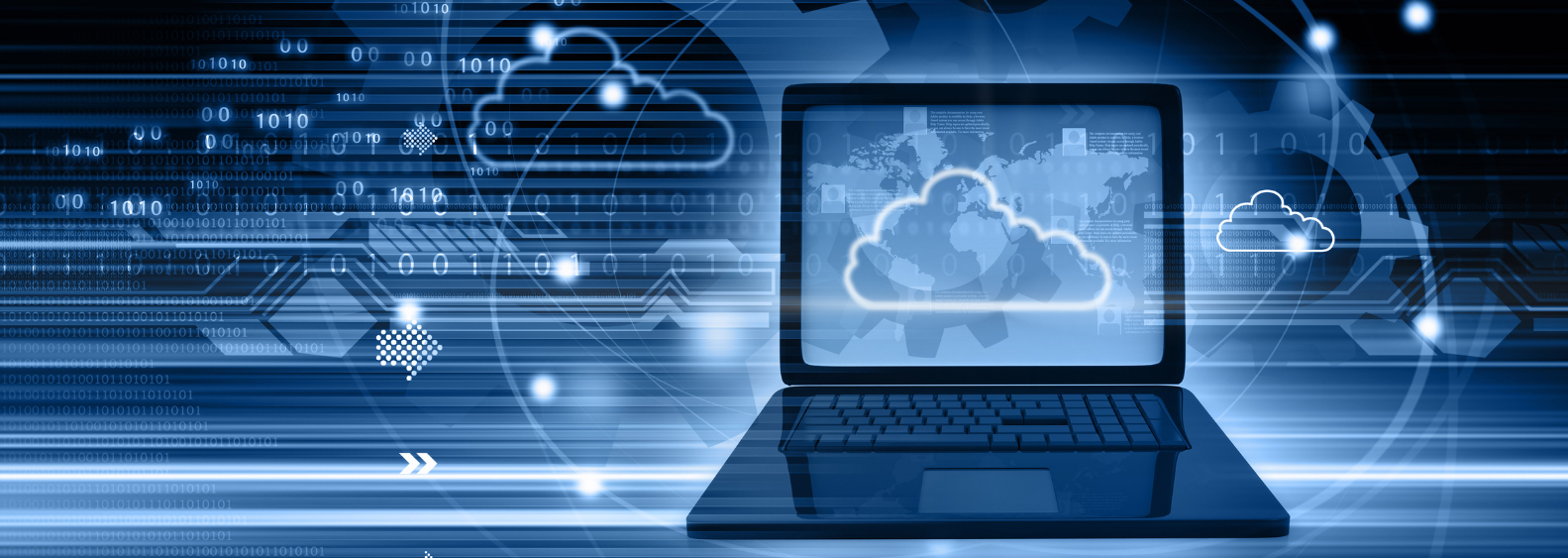
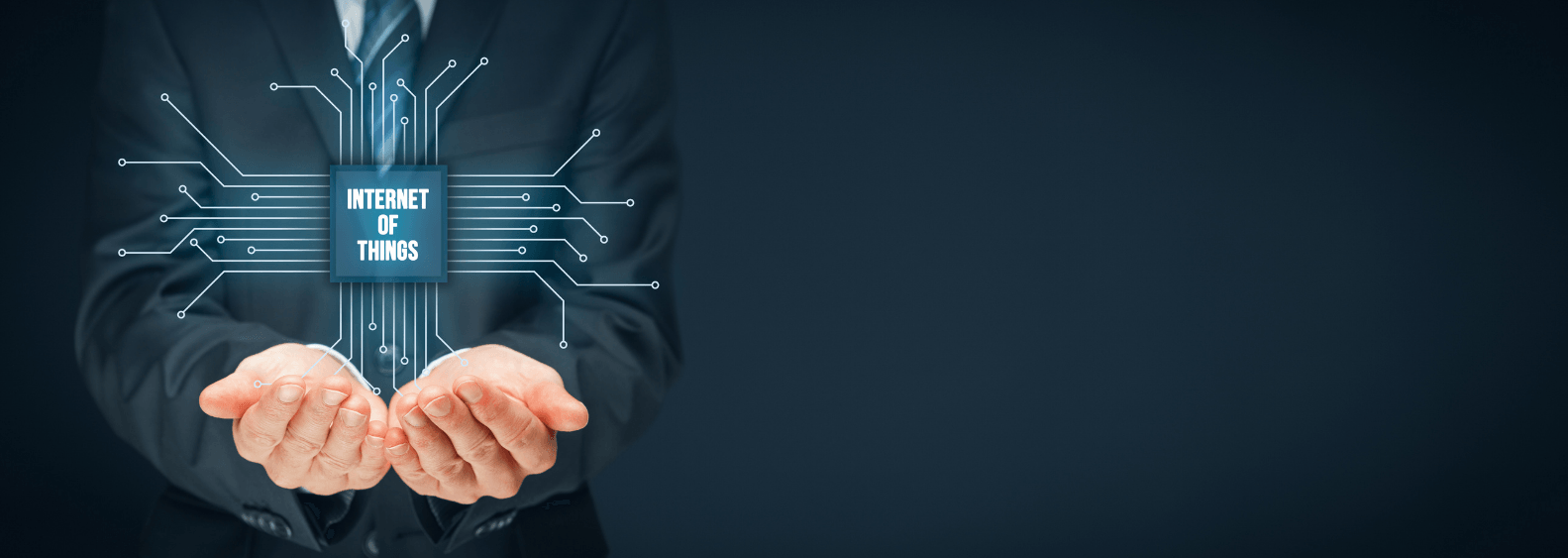