Self-Service Data Studio Case Study
SELF SERVICE DATA STUDIO CASE STUDY
This case study showcases GEMBO, a leader in SaaS Industrial IoT Platforms, enhancing a global manufacturer's operations by deploying its Precare Data Studio BI product across 70 machines. The solution, focused on self-service data management and analytics, resulted in significant manpower savings, improved self-service efficiency, and automated analytics distribution. Unique to GEMBO Precare is its ability to deploy independent sensors, connecting any machine to its cloud, thereby offering predictive maintenance and operational insights without substantial capital expenditure, distinguishing it from other market solutions.
REQUEST CASE STUDY
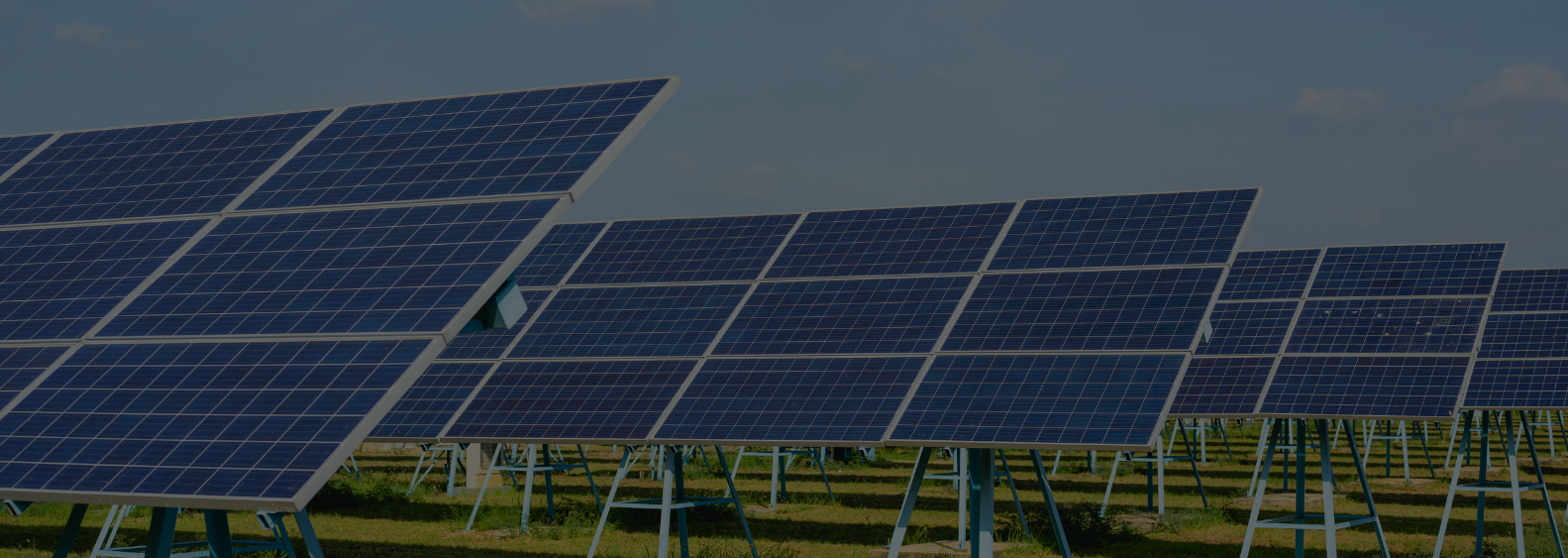
GEMBO ( www.gembo.co ) has a SaaS Industrial IOT Platform which provides enterprises and users with mission critical data, insights and decision making tools enabling cost reduction and revenue growth through optimization via the use of IoT, Artificial Intelligence and Machine Learning. Farm Operator Intro A large-scale solar farm operator, managing a 50 MW solar farm with significant investments in infrastructure. The solar farm has a current efficiency of 24% and a target of increasing this efficiency over time. The farm operates in an area where electricity prices are approximately $32 per MWh, and it has a large operational budget dedicated to maintaining its equipment. GEM has deployed the Precare cloud, predictive maintenance and solar power prediction Package, on the customers Data, extracted from the solar farm's SCADA system. Problem Due to the complexity of solar equipment and environmental factors, the customer has faced a gradual decline in efficiency, dropping from 26% to 24% over the past few years. As a result, the farm's revenue has been impacted by lower power output, and operational expenses have been steadily increasing. Furthermore, the lack of predictive maintenance (PdM) has led to frequent downtime and unplanned maintenance, further increasing the inefficiencies. The farm owner reached out for a solution that could improve operational efficiency, reduce costs, and enhance overall power production by using predictive analytics to forecast and mitigate potential issues before they occur. Solution After evaluating the farm’s needs and existing system, GEM’s Predictive Maintenance (PdM) and Solar Power Prediction packages were discussed and found as the right fit. This solution was implemented through GEM’s Precare analytics platform, which helps monitor and predict performance, detect faults early, and optimize maintenance schedules. The key components of GEM’s solution included: Real-time Monitoring: Continuous monitoring of solar inverters, panels, and environmental conditions. Predictive Maintenance: Advanced machine learning models to predict the likelihood of system failures and performance degradation. Power Output Forecasting: Predictive analytics to model expected energy production based on historical data and real-time inputs, leading to more accurate forecasting and optimizing grid management. Results After deploying GEM’s predictive maintenance and power optimization system, GEM provided the customer a calculation of a 3 year business analysis Financial Benefits: Revenue Increase: The system’s efficiency would increase by an additional $864,320 in revenue over 3 years due to the increased power output from the higher efficiency (25% vs. 24%). OPEX Reduction: Predictive maintenance would reduce the monthly operational expenses by 3%, leading to OPEX savings of $78,810 over the 3-year period. Net Benefits: The customer will realize a total net benefit of $758,130 after deducting the initial system cost and subscription fees. ROI: The ROI of 658.13% was computed from the net benefits of $758,130 after accounting for system cost investments.
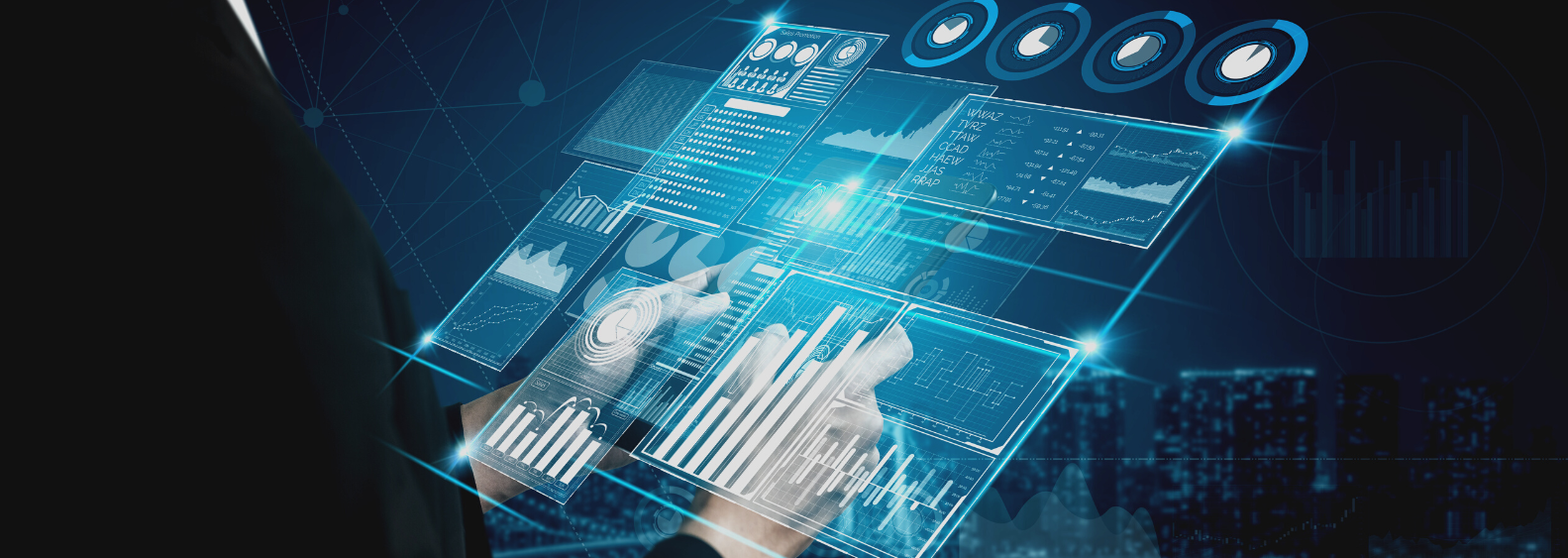
GEMBO ( www.gembo.co ) is a leading innovator in the world of SaaS Industrial IoT Platforms, with a proven track record of delivering cutting-edge solutions that help customers achieve their business goals. The company's platform uses a combination of IoT, machine learning, and AI to provide customers with real-time insights into their operations, enabling them to make better decisions and optimize their performance. GEMBO is committed to continuous innovation, and the company is constantly looking for new ways to use technology to help its customers succeed. Customer Intro The customer is a multi $B Tier one manufacturer, with multiple factories around the globe. Manufacturing lines vary between electronic manufacturing to semiconductor, serving a variety of markets including Automotive, Networking, Industrial, Audio and Gaming. GEM has deployed Precare Cloud , Precare Edge , OEE Availability and predictive analytics Package . Its footprint grew from a few machines to over 90 machines in a few of their factories. Problem The customer has been utilizing OEE Availability analytics to identify machines with low availability and assigning them to responsible technicians. The customer's management team has been overwhelmed with emails from technicians providing status updates on the machines after they have taken corrective actions. The customer intends to streamline the process of monitoring machine status from the receipt of OEE Availability status to the resolution of availability issues, enabling the machines to operate efficiently based on established availability KPIs. The customer has provided the following workflow to illustrate their requirements.
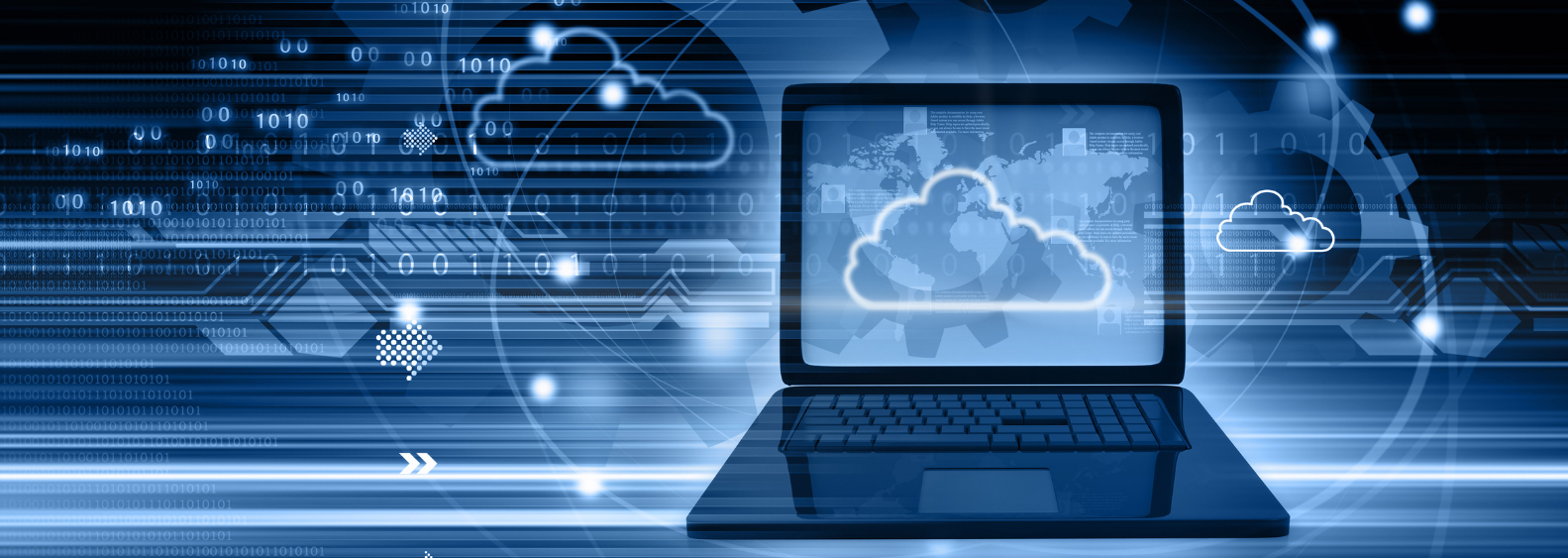
GEMBO ( www.gembo.co ) is a leading innovator in the world of SaaS Industrial IoT Platforms, with a proven track record of delivering cutting-edge solutions that help customers achieve their business goals. The company's platform uses a combination of IoT, machine learning, and AI to provide customers with real-time insights into their operations, enabling them to make better decisions and optimize their performance. GEMBO is committed to continuous innovation, and the company is constantly looking for new ways to use technology to help its customers succeed. Customer Intro The customer is a Tier 1 multi-billion dollar global manufacturing leader in the power, discrete semiconductor, and passive electronic components (PES) space. GEMBO has deployed a suite of innovative, cloud-based solutions to the customer, including Precare Cloud, Precare Edge, OEE Availability, Performance, and Quality packages. These solutions have been deployed to 70 machines across two factory floors, and the customer intends to scale the deployment across their entire Asia-Pacific footprint. Problem The customer's equipment engineering team has been managing the productivity of their machines through manual Excel reports. These reports are prepared by machine operators, checked and consolidated by supervisors, and then reported to management by factory floor managers. The customer needs to minimize or eliminate these manual reports to improve the accuracy of the reports and save on manpower costs. The following are examples of manual reports that the customer needs to eliminate: 1. Calculation of the share of subcategories of Performance and Quality 2. Calculation of the percentage of Planned Downtime to Total Run Time 3. Graphical presentation of OEE Availability with Time Frame These reports are time-consuming and error-prone. They also require a significant amount of manpower to create and maintain. By eliminating these manual reports, the customer can improve the accuracy of their productivity data and save on manpower costs. Solution After a technical discussion with the customer, GEM integrated the manual Excel reports into the OEE analytics framework. The team then implemented the following process: Define the customer requirements Gather the excel reports Create an output image showing changes in the analytics Define data to be collected Collect data from the customers Collect the data from customer Validate the completeness of the data based on the requirements Collect missing data Confirm with customer if all data are accurate and structured properly based on their requirements Prepare the design Overview Customer Requirements Use Case System Diagram Code Diagram Review and approval of the design Testing on Developer Environment Deployment to Production Customer acceptance Results The migration of previously manually prepared OEE reports to a digital format using OEE Analytics resulted in the following benefits: 100% savings on manpower costs, as the reports are now generated automatically and do not require manual input. 100% accuracy, as the data is collected directly from the machines and is not subject to human error. 100% time savings for management, as they no longer need to spend time reviewing and validating the reports. Improved decision-making, as the Operations Group can now access real-time data and insights to make better decisions. Increased efficiency, as the Operations Group can now focus on core tasks and not on data entry and reporting. Conclusions GEMBO Precare has a set of powerful data acquisition, analytics, predictive and OEE tools for manufacturing equipment. GEMBO Precare compiles critical KPIs that can be used to easily trace back which machine or machine subsystem is responsible for a low KPI score. GEMBO Precare is also able to make predictions at equal or better than humanly possible for machine maintenance to be scheduled before a failure occurs. But most importantly, unlike other market solutions, GEMBO Precare is able to deploy its own sensors independently from any machine controller and fully connect any machine data island to the GEMBO Precare Cloud at a fraction of the cost of a new machine; hence, saving manufacturers from having to make large and risky CAPEX and OPEX investments for new machines. Contact Us Visit us at www.gembo.co or contact us via email at sales@gembo.co
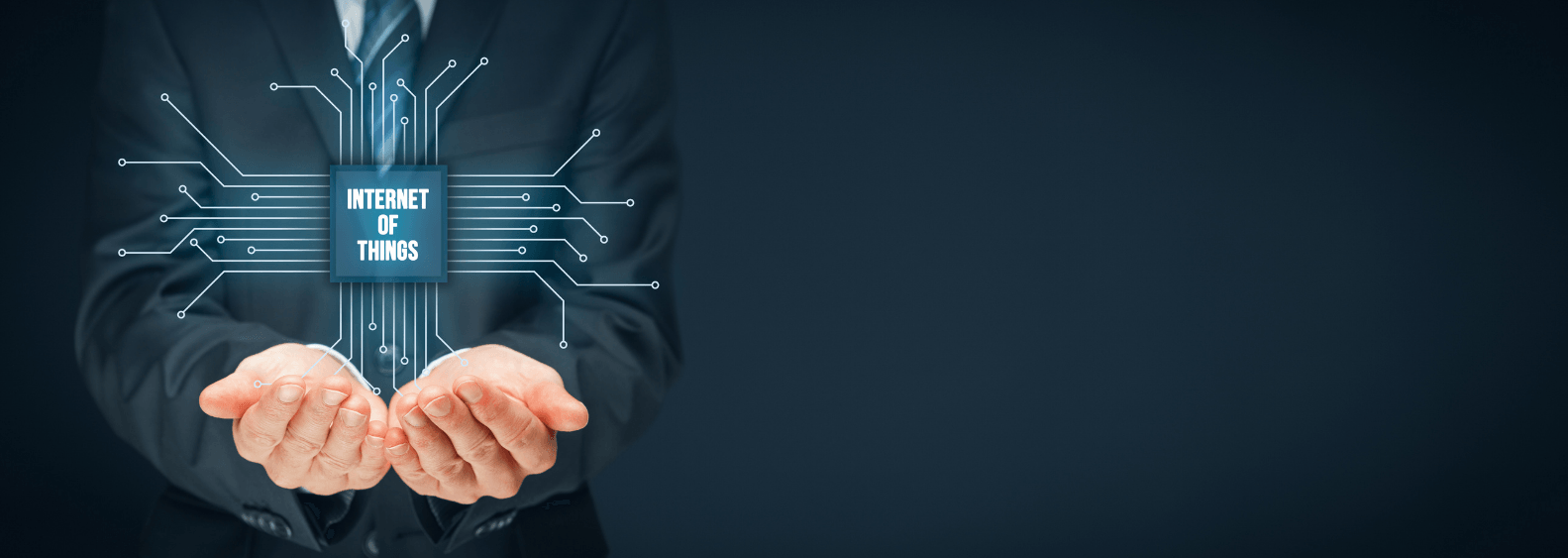
INTRODUCTION The GEMBO PRECARE platform enables manufacturers to seamlessly make the transition to Industry 4.0 literally overnight, while keeping their investments in legacy machines; thus, being able to tap into the potential of real-time access to machine data in order to improve efficiency, productivity and quality. Real-time access to machine data can be through any combination of sensors, serial and parallel port interfaces, Ethernet and sensors, no matter where the data is originating from, i.e., directly from the machine, or indirectly from a PLC or a data store on a network. Complex event process control at the edge of the cloud or at the machine itself requires hardware platforms with adequate processing power. GEMBO Precare supports edge processing through the use of powerful software agents. These agents take full advantage of the capabilities of the underlying hardware. In this white paper we show how the GEMBO Precare Industry 4.0 IoT platform takes advantage of Intel® x86 processor and Intel® Altera® Cyclone V SoC FPGA hardware capabilities to implement process monitoring and control at the edge in an industrial flow control application. GEMBO PRECARE MOTOR CONTROL AGENT Motors used in machines and production processes are very common and the ability to monitor them in real-time is understandably of crucial importance. GEMBO has developed an end-to-end motor control and monitoring solution in collaboration with Intel® and B&R Automation®, which takes advantage of the versatile and powerful GEMBO Agents for CEP at the edge and the GEMBO Precare cloud platform for monitoring and predictive maintenance. The process diagram shown below depicts a flow control application example. Control of a pump controls the flow rate in a pipe, and a safety valve prevents overpressure inside the pipe.